A fondo. Industria 4.0: digitalización, eficiencia y flexibilidad
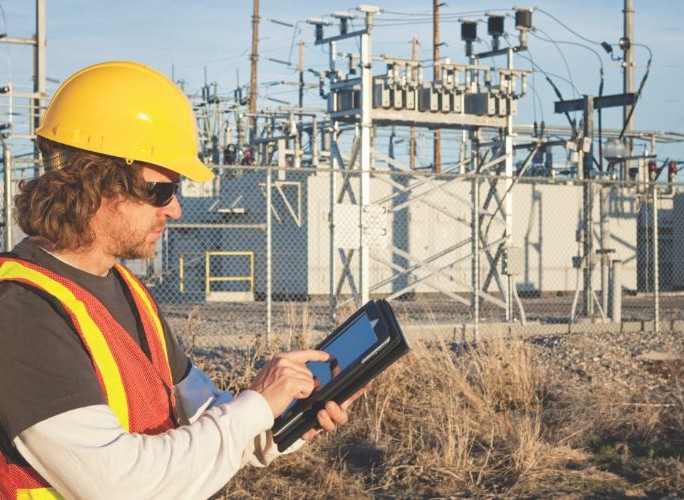
La Cuarta Revolución Industrial está dando paso a la industria 4.0, protagonizada por fábricas inteligentes, digitales, más eficientes y capaces de adaptarse mejor a la demanda del mercado.
La introducción de la máquina de vapor de James Watt marca el comienzo de la Revolución Industrial, con la que arranca un periodo de honda transformación tecnológica, económica, social y demográfica. El ferrocarril, el barco de vapor y la industrialización transformaron el viejo mundo rural, basado en la agricultura y el comercio, en un nuevo mundo urbano e industrial.
A finales del siglo XIX y hasta el comienzo de la Primera Guerra Mundial se produjo la Segunda Revolución Industrial, con la implantación del modelo de producción en masa, la utilización de nuevas energías –gas, petróleo y electricidad- y el desarrollo de nuevos sistemas de transporte –automóvil y avión- y de comunicación –radio y teléfono- que redujeron las distancias, dando pie a una incipiente globalización.
La Tercera Revolución Industrial llegaría con la Revolución Digital que produjo el desarrollo de los sistemas informáticos y el paso de una tecnología analógica y mecánica hacia una tecnología digital. Y con este replanteamiento todavía en curso, se empieza a hablar ya de una Cuarta Revolución Industrial, que da lugar a la denominada ‘industria 4.0’, basada en una nueva forma de organizar los medios de producción, merced al desarrollo de fábricas inteligentes, digitales, más eficientes y con una flexibilidad que les permite adaptarse a las necesidades concretas del mercado.
¿Qué es la industria 4.0?
La consultora EY, en su ‘II Termómetro del middle market en España. Expectativas económicas y de negocio’, afirma que “las nuevas tecnologías y, en especial, el Internet de las Cosas, juegan un papel central en la denominada Industria 4.0, un concepto clave de la Cuarta Revolución Industrial. Éste se basa en el uso intensivo de las nuevas tecnologías con el fin de desarrollar factorías más inteligentes, respetuosas con el medio ambiente y con una mayor capacidad de planificar una producción más acorde a las fluctuaciones de la demanda”.
La empresa de servicios de ingeniería industrial Sisteplant explica que la nueva era digital plantea desafíos como “la personalización en masa, la necesidad de reducir los costes de producción, la disminución de los plazos de salida al mercado, la transformación digital, la interconectividad y la necesidad de hacer evolucionar el papel del personal de planta”.
Así pues, considera que los pilares en los que debe basarse la ‘fábrica del futuro’ son tres: “una estrategia industrial dirigida a lograr una robustez y agilidad extrema; unas tecnologías de la información que permitan alcanzar un modelo híbrido entre el mundo físico y el virtual -machine learning, realidad aumentada, realidad virtual y procesamiento de información en tiempo real-; y una redefinición del papel que deben jugar las personas y de las capacidades que deben adquirir”, a partir de “una evolución de los profesionales para que se conviertan en 4.0”.
KPMG precisa que la industria 4.0 tiene que ver con la conectividad. La consultora opina que “es una oportunidad para cambiar radicalmente la manera en que la industria responde a las necesidades de la sociedad”. Asegura que “el avance de la industria 4.0 estará impulsado por un entorno inteligente, interconectado y generalizado”, gracias a tecnologías como big data, impresión 3D, robótica, sensores, realidad aumentada, inteligencia artificial o machine learning. Y el estudio ‘Industry 4.0: Building the digital enterprise’, de PwC, añade otras tecnologías, como cloud computing, Internet de las Cosas, sistemas de localización, interfaces avanzadas hombre-máquina, sistemas de autentificación y detección del fraude, perfilado multinivel del consumidor y de su interacción o los wearables.
Industria 4.0 en cifras
El citado informe de PwC señala que el sector industrial global invertirá un total de 907.000 millones de dólares en la transformación digital en el periodo 2015-2020. Sin embargo, la consultora reseña que España todavía no está en este escenario, ya que nuestras compañías industriales están claramente por detrás de las empresas del resto del mundo en esta materia. Así, sólo el 8% de las empresas industriales de nuestro país se encontraban en un nivel de digitalización avanzado al inicio de dicho periodo, muy lejos del 33% del sector a nivel global.
Además, advierte que la velocidad del proceso de digitalización también es menor en España. La consultora prevé que el porcentaje de compañías industriales digitalmente avanzadas en España llegará al 19% en 2020, frente al 72% que alcanzará en el resto del mundo.
Por otra parte, PwC asegura que las compañías industriales digitalmente avanzadas experimentarán un incremento medio de su facturación anual del 2,9% durante el periodo 2015-2020. De esta manera, los encuestados esperan ingresar 493.000 millones de dólares adicionales al año gracias a la digitalización. En el caso de España, este impulso adicional de los ingresos será más reducido, en torno al 1%.
Además, PwC adelanta que la reducción media anual de los costes operativos será del 3,6% hasta 2020. Y los niveles de productividad podrían aumentar un 4,1% de media cada ejercicio. Las empresas consultadas en el estudio estiman que ahorrarán 421.000 millones de dólares al año por la reducción de costes que originará la digitalización. En el caso del sector industrial español, la rebaja media anual de los costes en este periodo será del 2%. Y el incremento de la eficiencia será del 2,2%.
“Las empresas del sector industrial deben apostar firmemente por procesos de transformación digital para mejorar la eficiencia y el aumento de la productividad, integrando y optimizando la gestión de las cadenas colaborativas de valor entre empresas”, anota la consultora. E incide en que “la digitalización e interconexión de productos y servicios –como los servicios asociados al Internet de las Cosas- pueden ayudar a las compañías a alcanzar importantes mejoras en su desempeño”.
Aprovechar las oportunidades
¿En qué se concreta la digitalización? Según indica el informe ‘The Fourth Industrial Revolution is here—are you ready?’, elaborado por Deloitte, el 57% de los encuestados piensan que su mayor potencial radica en el desarrollo de productos comerciales, permitiendo incrementar la productividad en un 56%. Pero la industria 4.0 también promete mejoras en el aprendizaje continuo, aprovechamiento de nuevas fuentes de talento, llegada a mercados desatendidos, aprovechamiento de herramientas predictivas para mejorar los procesos y reducir riesgos o conexión de las cadenas de suministro, permitiendo sistemas más ágiles.
KPMG afirma que las oportunidades para la disrupción son numerosas: rapidez sin precedentes para llegar al mercado, desarrollo de productos competitivos y diferenciación en precio, conocimiento íntimo de los consumidores, expansión de nuevos servicios o modelos de negocio, mejora de las operaciones, etc.
Por otro lado, el 87% de los directivos encuestados por Deloitte consideran que la industria 4.0 conducirá a más igualdad y estabilidad. Y tres cuartas partes de los consultados dicen que las empresas tendrán mucha más influencia que los gobiernos y otras entidades en la configuración del futuro.
¿Preparados para la revolución?
Estamos dando los primeros pasos hacia esa industria 4.0, pero la transición no es tan sencilla. Si atendemos a las conclusiones del citado informe de Deloitte, parece que todavía queda mucho camino por delante. Según el mismo, sólo el 14% de los encuestados confía plenamente en que sus organizaciones estén listas para aprovechar por completo los cambios asociados con la industria 4.0. Y apenas el 25% de los directivos consultados cree que dispone de la fuerza laboral y los conjuntos de habilidades necesarios para el futuro, a pesar de que el 84% afirma que está haciendo todo lo posible para crear una fuerza de trabajo para la industria 4.0.
PwC precisa que la digitalización está siendo más lenta en la industria española por la falta de cultura digital y de una formación adecuada (según el 76% de los consultados), la ausencia de una visión clara de las operaciones digitales y del liderazgo de la alta dirección (64%) y un conocimiento confuso de los beneficios económicos que supone invertir en tecnologías digitales (56%).
Asimismo, los directivos consultados por EY reseñan que los principales retos a los que se enfrenta el desarrollo de la industria 4.0 son la ausencia de personal cualificado para poner en marcha las innovaciones que conlleva, así como el riesgo que comporta tener que modificar el modelo de negocio de la compañía o la dificultad para la asimilación de los cambios por parte las empresas y los empresarios.